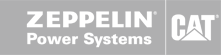
With data analyses in the FOC to Predictive Maintenance
“100 percent power!” This claim does not just apply to the performance of the modern Cat and MaK engines that Zeppelin Power Systems distributes as an official partner of Caterpillar. But it also applies to our service for drive and energy systems, which is based on the principle of maximum reliability. Against a backdrop of digital solutions transforming the market, the company has now positioned itself with a Fleet Operations Center (FOC), which was implemented in collaboration with the control room experts from JST – Jungmann Systemtechnik®. The oft-quoted slogan “data is the new gold” rings true.
A cruise ship in the Mediterranean or on a river, a container freighter, a locomotive or special machinery in use. Reliable engine operation is a basic prerequisite for trouble-free workflows and processes.
Precise forecasts for maximum availability
Continuity and reliability – this is where Zeppelin Power Systems comes in. Remote monitoring is the magic formula that enables the company to provide its customers with precise forecasts on the condition of their engines and improve the availability of their equipment. Be it marine engines or drives for locomotives, combined heat and power plants or engines for special machinery – based on data analysis and alarm monitoring, Zeppelin Power Systems offers a supplement to customized service to avoid unwanted and costly failures.
The FOC collects and analyzes engine data 24/7 worldwide
The central pillar of this concept is the Hamburg Fleet Operations Center (FOC), where the engine specialists relied on the know-how of the JST control room team for its implementation. There, the data from all globally connected drive and energy systems are received 24/7 for evaluation. The hardware and software solutions implemented by JST not only allow error messages to be recorded in real time, they also go one step further: Supported by innovative technical solutions, the engine operator can be given proactive information in order to achieve significantly higher equipment availability.
Starting signal for the dawn of the Predictive Maintenance era
“The construction of the control room went hand in hand with the first major service digitization projects within the company,” explains Andreas Jantzen, Head of FOC and Helpdesk. A special requirement at the start of the new predictive maintenance era: “We were looking for an experienced partner who could offer us state-of-the-art solutions,” says project manager Jantzen, “Jungmann was able to provide considerable expertise and convincing reference projects; with their project in the operations center of a cruise shipping company, we even have a joint customer.
Ready for expansion in the future
The technical possibilities of the JST components immediately appealed to the marine operations engineer: “We deliberately thought big with an eye to future digital services.” We wanted to position ourselves so that we could expand in the future, and the Jungmann solutions were an excellent fit. It was immediately clear to Andreas Jantzen during his visit to the JST control room simulator: “Consultant Dirk Lüders presented us with professional options that would allow us to implement our wishes to perfection. It was very impressive to see what was hidden behind the façade of an office building.”
One system, one button – everything under control
The Fleet Operations Center was constructed by Jungmann Systemtechnik in two expansion phases. The Zeppelin Power Systems team benefits from more than just ergonomic control room furniture. Of particular importance is the user-friendly MultiConsoling® technology, enabling all systems to be conveniently available at any workstation at the touch of a button and displayed for shared use via the intuitively operated Videowall.
MultiConsoling® - "a really smart solution"
“Efficient, fast and uncomplicated – MutiConsoling® is a really smart solution. It helps us to be able to precisely assess the situation in the individual systems that we monitor. Groups of visitors are also regularly impressed by the range of applications in combination with the large display wall,” reports Andreas Jantzen.
Qualified support on technical issues
And because everything at the Fleet Operations Center revolves around perfect customer service, the FOC Head also took a close look at Jungmann Service. Jantzen: “We have received qualified support for every technical question. It is really all very professional.” He also considers the JST Academy seminars to be particularly worth recommending. “It’s a valuable experience – you get a much deeper understanding of the system there thanks to expert answers.”
Andreas Jantzen sums up: “Intervene before there is any damage – we are now much closer to this goal with the solutions from JST. The FOC serves as our business card, so to speak, and demonstrates our expertise in the digitization of service to our customers.”
JST consultant Dirk Lüders provided technical support for the FOC project and is confident:
“Especially in view of the future challenges for service optimization, the Fleet Operations Center has created the best conditions for preventing revenue losses due to machine failures. Data analyses provide the desired basis for detecting defects in propulsion systems long before they occur.”
Our references today (selection)
A
B
C
E
H
I
M
N
P
R
S
- s.Oliver, Rottendorf
- SachsenEnergie, Dresden
- SAG, Berlin
- SAG, Nürnberg / Nürnberg Messe
- Salzgitter Flachstahl
- Senvion SE, Osterrönfeld
- SGL Carbon Group, Bonn
- SIEMENS
- SIEMENS, Wegberg
- Spenner, Erwitte
- Städtische Werke Magdeburg
- Stadtwerke Gießen
- Stadtwerke Ratingen
- Stadtwerke Schwerin, Kraftwerk Süd
- Stadtwerke Steinburg GmbH, Itzehoe
- Stadtwerke Wolfenbüttel
- Starlim Sterner, Marchtrenk
- STORAG ETZEL, Friedeburg
- Straßenverkehrsamt Frankfurt am Main
V
Unsere Referenzen (Archive)