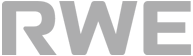
Central control center for opencast lignite mines in the Rhenish mining area opens up synergies
Taking a big step forward to meet the increasing challenges in the control room sector – this is the goal that RWE Power AG has set itself in the Rhenish mining area, the largest lignite mining zone in Europe. The increasing economic pressure associated with the coal phase-out also requires the development of further synergies in the monitoring of opencast mining operations. Together with the experts from JST – Jungmann Systemtechnik®, an innovative control room was implemented in which the operational monitoring of three coal mining plants is centralized and bundled.
Huge steel giants that can move an entire truckload with a single shovel – the images of the impressive bucket wheel excavators from open-cast mines are well known. But how and by whom are these giants actually moved? In RWE Power AG’s three control rooms Garzweiler, Hambach and Inden, qualified operators ensure that all the cogs in the process chain mesh and that the right response is given to tasks such as “Restart conveyor system!” or “Equipment has fallen off!”.
Competence is bundled through centralization
Economic pressure and a declining number of skilled workers are the challenges facing the opencast mines in the Rhenish mining area today. The solution: In collaboration with the JST control room specialists, a new central control station was installed in which colleagues from the three operational monitoring sites share responsibility for opencast mining in the lignite mining area. This pooling of resources enables personnel synergies to be leveraged.
Technical flexibility triggers synergy effects
Here it is possible to meet all requirements with a shift group reduced from seven to five men. The dispatchers benefit from a technical concept that makes their work much easier thanks to maximum clarity and flexibility. It is precisely this flexibility that triggers knowledge transfer and synergy effects, as the employees support each other with the tasks in the control room.
"We are open for new ways"
Project manager Andreas Rott remembers the initial phase of the project: “The acceptance of my colleagues was very important to me. The reference to JST and the desire to take a closer look at the Jungmann solutions came from the circle of employees. We had already looked at the JST system in the past. Even back then, many people thought the concept and presentation were great and were downright sad that we had decided against it. But at that moment, the time was simply not yet ripe for us. We thought that there had to be a separate monitor for each application. That’s why we made a different decision at the time. Today we see that this idea is outdated. We are open to new ways.”
Integrated overall concept based on the JST myGUI®
These “new ways” that RWE is taking with the central control room are given a solid foundation by JST: Based on the myGUI® user platform, which was specially developed for control rooms, an integrated overall concept enables fast and demand-oriented access to all almost 100 sources of the control room – without changing locations and without constant connection of all applications. Relevant systems automatically report to the operator via the components of the KVM solution MultiConsoling®, who decides individually which application he needs at his workstation at what time.
This ensures future-proof Scalability
With MultiConsoling® it was possible to reduce the eleven screens at the operator console to five monitors. Each workstation has an identical design and can be expanded with additional applications to ensure future-proof scalability. Even in the event of further extensions, no changes to the front end are necessary. In addition, three individual display walls with modern video wall technology offer further views for the entire shift group. “The video walls serve as a real TeamView,” confirms Andreas Rott.
Control center before and after renovation.
Visual and audible alarm options
In the control room developed together with JST, further employee wishes could be realized: For example, the OPAL X11® ceiling sail installed above each control room desk ensures a secure alerting process on two levels. The operators are visually warned in critical situations via the color change of the AlarmLight. They also receive acoustic signals, which are only received by the relevant employee via directional loudspeakers.
Preset can be called up at any place
The login process with the myLogin® software, also developed by JST, is also rated as user-friendly and uncomplicated. Andreas Rott: “With the card, everyone can create their own favorite setups. We were able to save ourselves rounds of coordination as to which setups might be necessary. The card is used more or less like a standard configuration memory, a preset that can be recalled at any time and in any place at lightning speed just by placing it into position.”
"Needed a 24/7 reliable partner"
Looking back, project manager Rott gives the cooperation with JST top marks: “The collaboration was great! We developed everything together. It was an extensive project with many specifications that spanned a period of one and a half years. We needed a 24/7 reliable partner for this. We also had to continue ongoing operations. And a service level agreement was necessary too. Not many providers on the market can do that.”
You are currently viewing a placeholder content from YouTube. To access the actual content, click the button below. Please note that doing so will share data with third-party providers.
More InformationOur references today (selection)
A
B
C
E
H
I
M
N
P
R
S
- s.Oliver, Rottendorf
- SachsenEnergie, Dresden
- SAG, Berlin
- SAG, Nürnberg / Nürnberg Messe
- Salzgitter Flachstahl
- Senvion SE, Osterrönfeld
- SGL Carbon Group, Bonn
- SIEMENS
- SIEMENS, Wegberg
- Spenner, Erwitte
- Städtische Werke Magdeburg
- Stadtwerke Gießen
- Stadtwerke Ratingen
- Stadtwerke Schwerin, Kraftwerk Süd
- Stadtwerke Steinburg GmbH, Itzehoe
- Stadtwerke Wolfenbüttel
- Starlim Sterner, Marchtrenk
- STORAG ETZEL, Friedeburg
- Straßenverkehrsamt Frankfurt am Main
V
Unsere Referenzen (Archive)