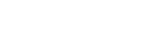
Control room transformation optimized energy supply at VW Commercial Vehicles
Vehicle construction, component manufacturing, infrastructure, heating plant – the facilities at the headquarters of the Volkswagen Commercial Vehicles brand in Hanover cover an area of 123 hectares. All the buildings on the site between the Mittelland Canal, railroad line and freeway have one thing in common: Two control rooms are responsible for the entire power generation and distribution, which have not only been optimized in a pioneering way thanks to innovative KVM technology from JST – Jungmann Systemtechnik®, but have also been linked together. The advantage: the entire team of control room operators now has an overview of the whole energy and media supply from a central location.
The images from the past are still vivid in the memories of many of those involved: The images from the past are still vivid in the memories of many of those involved: columns of screens several meters long lined up next to each other. Whether compressed air supply, cooling systems, boiler installations or the control of the ventilation systems – a total of 16 individual computers, usually with two monitors each, had to be kept an eye on by a single employee. “Due to the many separate monitors, it was a challenge to keep an eye on all the systems. We wanted a significantly improved overview and therefore greater efficiency,” reports Svenja Daubitz (Power Generation & Distribution, Volkswagen Commercial Vehicles).
Idea: a team in which know-how is collected
Expansion of sustainable production at a historically grown industrial site – this was the background against which those responsible for the “Control room for energy supply” project wanted to achieve two objectives at once. In addition to far-reaching technological modernization, it was also about employee interaction. The 25-strong control room crew, which was split into two work areas hundreds of meters apart called “Heating Plant” and “Sector 8”, was to be brought together to form a unified team. The aim was to create a genuine pool of knowledge in which the skills and expertise of all colleagues could be pooled.
In individual steps to the targeted goal
Together with the control room experts from JST, a solution for the reliable and efficient management of the energy supply in the automotive plant was found in several steps. Step one: The control room for the heating plant receives a comprehensive technical upgrade. The KVM controlling with JST MultiConsoling® and an extended SCADA visualization system are used. Significantly less monitors are now required for monitoring. The individual sources can be conveniently switched to any desired screen. The heart of this innovative control solution is located in the technical room: the MultiCenter.
"We noticed right away that it works well!"
In the next step, the other part of the control room team in “Sector 8” will receive a completely new control station, equipped with large-screen technology, ergonomic furniture and, of course, MultiConsoling® technology with its core element, the MultiCenter. “We first wanted to get a feeling for the technical innovations and started to control the plant on this basis,” explains Svenja Daubitz, “we noticed right away that it works well!”
Linking the control rooms via optical waveguides
At this point, it is now possible to accomplish what the project stakeholders had in mind from the outset. Optical waveguides link the MultiCenters of both control centers. More than 600 meters are bridged. A separate network is created. The cables transmit all signals over long distances at the speed of light and with enormous data capacity. The result: All applications can be operated from the new “Sector 8” control center. “We have direct access to all sources. The brain is in the heating plant and the execution works in Sector 8,” confirms Svenja Daubitz.
Employees and company benefit from
It is not only the employees who are responsible for the energy supply at the plant who profit from now working as a joint group from one location. The ambitious project also has advantages for the company: The bundling of expertise in a single control room makes it possible to deploy employees more effectively and, for example, to react more flexibly to interruptions. “The centralization of control rooms creates greater scope for personnel planning,” says JST Consultant Volker Weimer, “our innovative technology provides answers to questions that will increasingly arise in the future as a result of the shortage of skilled workers.”
Even small deviations suddenly become visible
Initial experiences with the merger and the technology upgrade show that there are other positive effects: The various systems report deviations and faults to the operator in a targeted manner that were previously overlooked. This not only allows irregularities to be identified more quickly, it also eliminates the unnecessary stress of monitoring the previously numerous individual screens. The team can focus its attention on examining the existing systems in detail.
Effective: Errors are solved faster
“The improved visualization has suddenly made things visible that nobody noticed before,” explains Svenja Daubitz. These include, for example, ventilation systems that have been improved in terms of energy efficiency and control technology. Conclusion: “With the new technology, we can not only track down such errors, we can also solve them more quickly.”
You are currently viewing a placeholder content from YouTube. To access the actual content, click the button below. Please note that doing so will share data with third-party providers.
More InformationOur references today (selection)
A
B
C
E
H
I
M
N
P
R
S
- s.Oliver, Rottendorf
- SachsenEnergie, Dresden
- SAG, Berlin
- SAG, Nürnberg / Nürnberg Messe
- Salzgitter Flachstahl
- Senvion SE, Osterrönfeld
- SGL Carbon Group, Bonn
- SIEMENS
- SIEMENS, Wegberg
- Spenner, Erwitte
- Städtische Werke Magdeburg
- Stadtwerke Gießen
- Stadtwerke Ratingen
- Stadtwerke Schwerin, Kraftwerk Süd
- Stadtwerke Steinburg GmbH, Itzehoe
- Stadtwerke Wolfenbüttel
- Starlim Sterner, Marchtrenk
- STORAG ETZEL, Friedeburg
- Straßenverkehrsamt Frankfurt am Main
V
Unsere Referenzen (Archive)